Paralleling Switchgear
Overview
States Manufacturing paralleling switchgear and control systems are designed, engineered and manufactured with customer’s specific needs in mind. Our goal is to deliver factory tested systems that provide custom tailored control and monitoring of power generation equipment. Systems are fully integrated with all components and features, to deliver a system with maximum uptime, reliability, and longevity as well as cost-of-ownership economy.
States experience working with all major generator manufacturers in conjunction with many different professional engineers allows us to provide cutting edge switchgear designs utilizing the latest in controls technology.
Paralleling controls and relaying available on Low Voltage Switchgear, Low Voltage Switchboards, and Metal-Clad Switchgear from States Manufacturing.
Industry standard types of paralleling power systems
- Backup/Standby Systems – When generation is applied only to serve as a back-up to the utility power source. These systems are popular in technology, healthcare, and life safety applications.
- Distributed Generation Systems – When generation is applied to either isolate the facility load from the utility source or remain in parallel with the utility source (peak shaving) to absorb changes in facility load. These systems typically serve as a back-up standby system as well to provide power in the event that the utility source is unavailable. These systems are popular world-wide and may offer significant monetary benefits depending on utility rates.
- Prime Power Systems – When generation is applied to act as the main, or only, source of power. These systems are popular in marine and military applications as well as remote sites where utility power is not available.
Features of States Manufacturing paralleling power systems:
- System designs offer the following transfer modes
- Open transition – Transfers between the utility source and generation source are accomplished by opening source before closing the other (break-before-make).
- Closed transition – Transfers between the utility source and the generation source are accomplished by closing both breakers together before one is opened (make-before-break). Synchronization is achieved in either an active (generation source is driven into voltage and phase lock with the utility source) or passive (generation source drifts into voltage and phase lock with the utility source.
- Softloading – Transfers between the utility source and the generation source are accomplished by closing both breakers together before one is opened (make-before-break). Synchronization is achieved by driving the generation source into voltage and phase lock with the utility source. Once both breakers are closed facility load is transferred either to or from the generation source at approximately 50kW per second.
- Continuous parallel – Utility source and generation source are synchronized by driving the generation source into voltage and phase lock with the utility source. The utility source and generation source remain in parallel and power is either exported or imported from the utility source. The generation source may also be run at a fixed, or base load, setting.
- Additional System Features (optional)
- Load demand control – When generators, in a multi-generator system, are taken off-line in a pre-determined sequence if the facility load does not require them. Functionality helps to reduce fuel and maintenance costs.
- Load add/shed control – When facility loads are either added or removed from the generation source in a pre-determined sequence based on generation source loading.
- Manual paralleling controls and protection to allow for bump-less transfers between utility and generation sources in the event of a component failure.
- Redundant “Hot-Standby” PLC controls – Two independent processors run in lock-step with each other with the secondary unit ready to take over in the event that the primary unit fails. Switchover from primary to secondary is seamless.
- Human-Machine Interface (HMI) panel provides interactive system oneline, expanded metering capabilities, data trending, alarm history, and remote control of system.
- Modbus TCP/IP remote communications to client owned monitoring equipment is standard. Many other communications protocols are available.
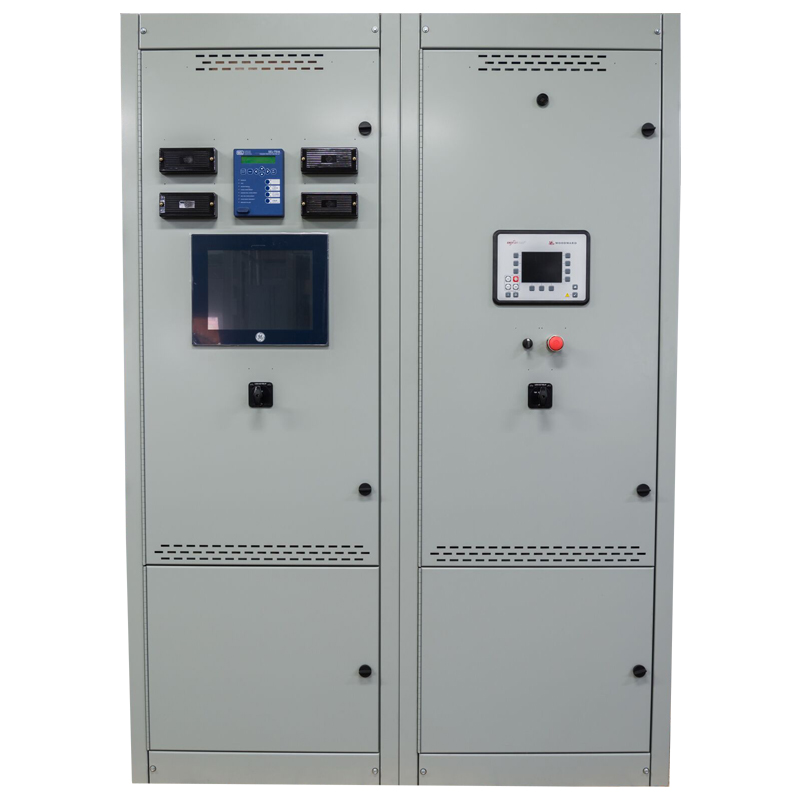
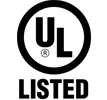